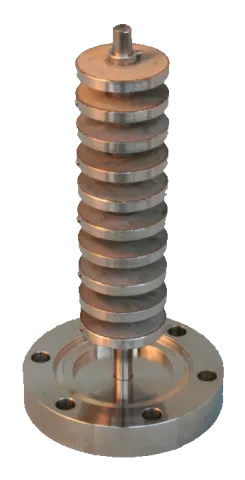
The non-contact atomization method yields spherical/high-purity NEG grains. The pumping speed is high, stable, and dust-free, because only coarse grains are collect on the fine wire mesh container, without being compressed and solidified.
Features
- Spherical grain
- Dust free
- Small self gas emission for XHV application
- High pumping speed for CO
- Ternary alloy Zr,V,Fe
- Adjustable pumping speed by number of disc (100 ~ 500 L/s)
- Removable sheath heater and thermocouple
- Any orientation
- No vibration, uncharged grain, no power
Specifications
Mounting flange | ICF70 (DN50CF) |
---|---|
Disc Size | 6.0g |
NEG /disc | 6.0g |
Pumping speed, per disc | H2 = 18, CO = 20, N2 = 7 L/s |
Pumping speed, H2 | 100 ~ 500 L/s |
Heater tube | 1/4" 316 St.St. |
Activation | 450°C, 30 min |
Connection | ICF70 (DN40CF) |
Height | 100 ~ 300 mm |
Weight | 450 ~ 600 g |
Maximum length of the heater and the TC is 4m.
Patented Technology
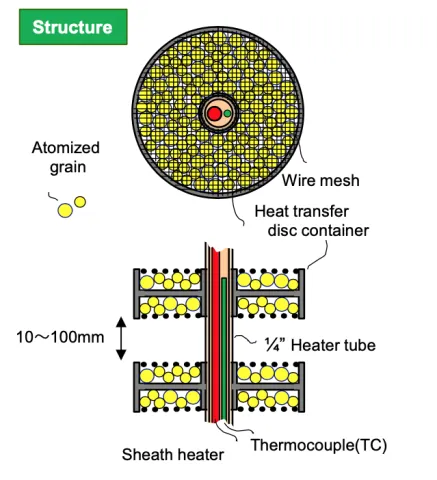
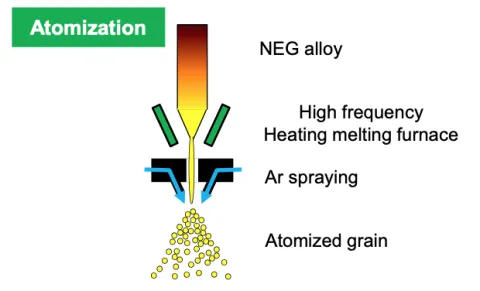
The Atomised Granule Non-Evaporable Getter (AG-NEG) pump is an innovative non-evaporable getter (NEG) pump that utilises NEG powder produced through advanced non-contact atomisation technology. The powder grains are used in their original form without compression consolidation. Due to the virtually spherical shape of the NEG particles and their highly stable surface condition, the pump exhibits high pumping speed and exceptionally reliable pumping characteristics.
The smooth, stable particle surfaces result in minimal self-gas emissions from the surface layer during repeated pumping cycles, making the AG-NEG pump ideal for achieving ultra-high vacuum (UHV) and extreme-high vacuum (XHV) conditions. Additionally, the use of relatively large grains with particle diameters around 100 µm allows the NEG particles to be thinly packed into a disc-shaped, heat-conductive container fitted with a 30 µm fine metal mesh, effectively preventing any risk of particle dispersion.
Furthermore, since the NEG particles are activated through conduction heating from a centrally positioned heater pipe (air side), radiant heat during activation is significantly minimized.
Difference from conventional NEG pumps
To utilize NEG alloy in getter pumps, it is necessary to increase the surface area for the absorption of gas molecules, making the powdering of the NEG metal essential. The NEG powders used in conventional getter pumps are obtained by mechanically crushing an ingot, collecting the resulting powder, and then employing methods such as:
- Thinly spreading the powder on a metal ribbon containing nickel as an eutectic,
- Adding a small amount of carbon and pressing it into a pill shape, and
- Mixing it with zirconium metal powder followed by vacuum sintering.
As a result of this process, the particle shapes are irregular with many protrusions (which aid in consolidation), the particle size distribution is broad (ranging from several micrometers to several hundred micrometers), and dust generation due to particle peeling during activation is unavoidable. Furthermore, since the crushed powder particles are consolidated again, the actual surface area is reduced, which also increases the cost of the NEG.
In contrast, NEG powder fabricated by atomization exhibits minimal variation in particle size, with particles being nearly spherical, greatly enhancing surface stability. However, bonding between the powder particles does not occur easily, making it impossible to construct a pump through compression consolidation as with conventional pumps.
To address this, we introduced a novel approach: instead of consolidating the NEG particles, we placed them into a metal mesh container with mesh holes smaller than the particle size to prevent dispersion into the air. As a result, we successfully developed a stable, low-cost, dust-free NEG pump with a high pumping rate per gram of NEG powder.
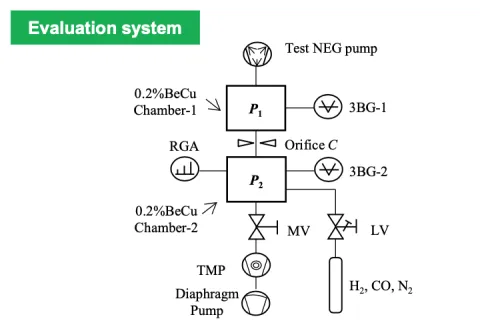

The performance of the AG-NEG pump
can be evaluated using a testing apparatus like the one shown in the diagram above. Since hydrogen (H2) diffuses through the NEG bulk, there is virtually no decrease in pumping speed, even during continuous operation. However, when gases such as carbon monoxide (CO) or nitrogen (N2) are pumped, they adsorb onto the NEG surface, causing a decrease in pumping speed. This reduction is reversible, as the pumping speed returns to its initial value after reactivation.
As a result, performance graphs for NEG pumps typically plot the accumulated pumped quantity Qt (m3·Pa), representing the total amount of gas absorbed, on the horizontal axis, and the pumping speed S (L/s) on the vertical axis. However, since CO and N2 degradation is negligible in ultra-high vacuum (UHV) and extreme-high vacuum (XHV) regions, our company uses pressure (Pa) on the horizontal axis to make it easier to interpret the pump’s characteristics.
It is important to note that the formula:
S1 = C [ (P2 - P2u) / (P1 - P1u) - 1]
(where P1u and P2u represent the ultimate vacuum pressures) can sometimes lead to the misunderstanding that the NEG pump is capable of achieving an ultimate vacuum of at least 10-11 Pa. To address this, a curve calculated using the formula:
S2 = C (P2/P1 - 1)
which represents the effective pumping speed without subtracting the ultimate vacuum, is also provided. This can serve as a guide to the ultimate vacuum achievable with the NEG.
Although the AG-NEG pumping speed characteristics shown in the graph above correspond to five discs, the pumping speed curves remain virtually proportional when the number of discs is increased.